News
The Pollboy In-Vessel Composting Facility: An Overview
Author: Dr Andrew Walsh PhD
Celtic Composting Systems Ltd. |
Project Manager: Mr Aengus Breathnach
Senior Executive Engineer
Galway County Council |
Introduction
Galway County Council in conjunction with Ballinasloe Town Council commissioned
the building of an in-vessel composting facility at Pollboy landfill to process
the domestic organic waste being produced within the administrative area of the
town council. An in-vessel system was chosen for the site given the superior
environmental and process control features offered by enclosed systems over conventional
open windrows. The facility was designed and installed by Celtic Composting Systems
Ltd, an Irish/US company that specialises in state-of-the-art composting systems.
The facility went into operation in March 2002.
The Composting Process
(1) Waste receipt
Organic kitchen and garden waste is delivered every other week to Pollboy. The
initial throughput of material represents the production from 1,500 homes, estimated
at between 400-600 tonnes per year. Some green waste that is delivered directly
to the landfill is also processed. Once weighed, the material is discharged onto
the floor of the covered tipping building and large contaminants such as refuse
sacks are removed. The protocol for the facility is for the immediate enclosure
of the waste material within the aerated composting reactors (ACRs) on the day
of arrival to avoid vermin, odour and leachate issues.
(2) Waste blending and loading
Once an initial inspection has been conducted, the material is loaded into an
auger mixer to blend the waste with bulking materials to allow the material
to be adjusted for moisture, nutrient ratio, porosity and microbial activity.
The blended "pre-compost" is then transferred to the ACRs by conveyor.
|
Fig. 1. The two reactors at the Pollboy facility. The inlet
and outlet air lines plus the leachate hose are illustrated. |
(3) The Aerated Composting Reactors
The reactors are designed to optimise the initial high-rate composting phase
through the enclosure of the composting biomass. On a 14 day cycle, the reactors
at the Pollboy facility are each rated at approximately 1-1.3 tonnes of pre-compost
capacity per day (365-475 tonnes per unit per year; Fig. 1). Air is delivered
to the reactors through a perforated floor with exhaust gases being drawn from
the void volume in the roof of the unit. The enclosure of the fresh material
at the start of the process offers a number of environmental advantages.
(a) Vermin are excluded during the initial phase while the material has a
high food value.
(b) All leachate is captured and directed to the leachate collection system.
(c) All exhaust gases are directed to a biofilter that removes off-odours.
(d) The reactors have a neat and tidy appearance
(e) Wind blown litter is eliminated.
(f) Rain is excluded and therefore water-logging of the biomass is avoided.
(4) Process control
The rate of air-flow through the reactors is dictated by temperature measurements
from within the compost pile that maintain composting conditions at an optimum
during this initial 14 day high rate cycle. This air-flow operates in two modes.
(a) Oxygenation mode supplies a sufficient air-flow to support aerobic respiration
in the reactors.
(b) Cool-down mode supplies air as a heat exchanger to cool the compost pile
when temperatures rise above optimum.
This "temperature feed-back" mechanism is automatically controlled
by a programmable logic controller (PLC) linked to proprietary CCS software.
The software continuously logs temperature within the reactors to document
that each batch has been pasteurised for quality control purposes. Automated
CO2/O2 feed-back analysis is also available to further enhance aerobic activity.
(5) Curing
At the end of the initial 14 day cycle the compost has been pasteurised and has
lost most of its food value. It is now safe to unload it into the curing bunker.
The curing bunker is an engineered composting system designed by CH2MHILL on
behalf of CCS. CH2MHILL is a world leader in compost engineering and the aerated
static pile (ASP) system can be used directly as a stand-alone composting technology
for lower priority materials such as green waste. However, for the purposes
of food waste, it is used as a secondary composting and curing system in conjunction
with the reactors. The compost is discharged from the reactors onto perforated
pipes that draw air under vacuum from the atmosphere through the piles and
this air is re-pressurised and forced through another biofilter to remove any
residual odours. In addition, all leachate and condensate is captured and directed
to the leachate interceptor system. The material is typically maintained in
the curing area for eight to 10 weeks prior to screening. Temperatures are
routinely monitored and the air-flow to each curing cell is subsequently regulated
by valves on the manifold pipe to optimise aeration and the temperature regime,
while avoiding over-aeration which can dry out the piles and waste electricity.
In this regard, the Pollboy facility is currently operating from a single-phase
domestic power supply.
Fig. 2. The C:N curing system illustrating the compost piles, aeration
lances and the biofilter at the far end of the bunker |
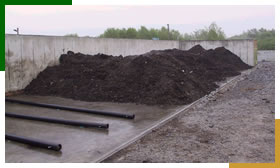 |
(6) Screening
At the end of the composting process, the compost is screened using a trommel.
The resultant material has a fine structure and is currently being beneficially
re-used as a soil conditioner and surface mulch in the Ballinasloe area.
 |
Fig. 3. The result material is a compost which can be used
as a soil improver for shrubs and plants |
___________________________________________________________________________________
The author acknowledges the kind permission of Mr Tom Kavanagh, Director of Environment & Conservation
Services, Galway County Council, to publish this article.
Back
|